Italian National Agency for New Technologies, Energy and Sustainable Economic Development
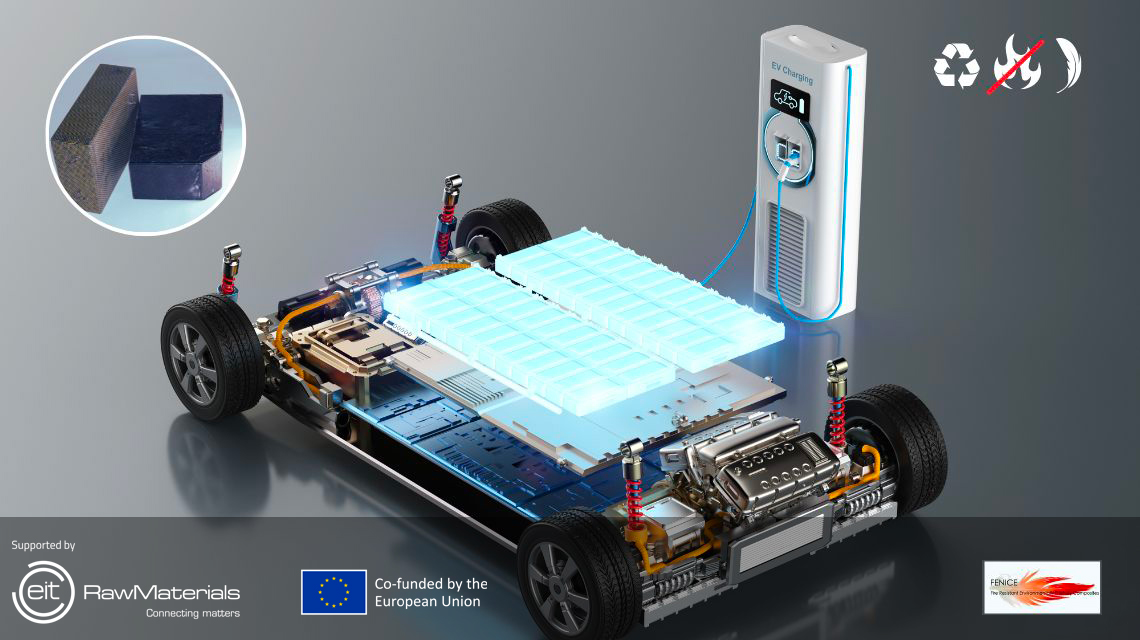
Transport: electric cars, new material for safer and more sustainable batteries
A new composite material for lithium batteries cases of electric vehicles to make them safer, more efficient and sustainable is the first outcome of the FENICE project[1], coordinated by ENEA, comprising 10 partners[2], including the Fiat Research Center (CRF).
The new fibre-reinforced composite material, developed at the ENEA laboratories, is based on a recyclable pre-preg[3] patented by the Italian company Crossfire, a project partner, and could be a promising alternative to the materials currently on the market in battery casing manufacturing.
In recent years car manufacturers, starting from sports car and racing sectors, have been engaged in a technological challenge to reduce the weight of vehicles, especially electric ones, increase their autonomy and contain CO2 emissions. So much so that the market for lightweight composite materials for vehicles is experiencing exponential growth. “Composite materials suitable for mass production, however, must be produced quickly and without generating waste or toxic substances” explained Claudio Mingazzini, researcher at the ENEA Faenza Materials Technologies Laboratory and coordinator of the project. “Furthermore – he said – the raw materials must be low cost, recyclable and, preferably come from a European supply chain”
The Italian company TACITA, specialized in motorcycles and electric vehicles, has already conducted a series of tests in real conditions and in the sporting sector, as a replacement for the current aluminum battery boxes, also on the motorcycles that participated in the Paris - Dakar 2024. This technology will soon be transferred to on-road motorcycles.
The battery box prototypes, developed as part of the FENICE project, use a new resin that has all these characteristics, created by Crossfire starting from PET, the plastic material of which common bottles are made. Thanks to an innovative formulation and design, the material has proven to meet the requirements to manufacture various structural components of electric cars, including the battery casing. The casing, made up of alternating layers of fibre-reinforced composite material and aluminium, also ensures high fire resistance.
“Although statistics show that electric vehicles are already much less likely to set on fire than their petrol and diesel equivalents, the aim is for increasingly higher safety levels, which also take into account road accidents, off-roads, flooding and fires caused by external sources. For these reasons the new battery boxes are designed to be resistant to the most extreme conditions" said the researcher.
“It is only a first result, but it is an important phase in accelerating electrification and decarbonisation of transportation means” concluded Mingazzini.
The FENICE project will also study possible applications of the same materials (and similar ones based on different resins) in sectors ranging from nautical to railways, from construction to wind power, always with the aim of combining mass production and sustainability.